یکی از راحت ترین و پر مصرف ترین و مهم ترین روشهای رایج برای شکل دادن به پلیمرها (بسپارها) استفاده از ماشین تزریق پلاستیک است.
پس از پیدایش و توسعه پلاستیکها تلاشها برای ساخت دستگاههایی که بتوان به وسیله آنها به سادگی مواد اولیه پلاستیک را به شکل دلخواه در آورد آغاز شد و به اختراع ماشینهای تزریق پلاستیک انجامید. اما قبل از ساخت ماشین های تزریق پلاستیک مدرن امروزی، کار شکل دهی به پلاستیکها خیلی مشکل بود ابتدا قالبهایی با صرف دقت و زحمات بسیار تهیه میشد و در گیرههای دستی تعبیه میشد و سیلندری با پیستون روی آن نصب میگردید و اطراف سیلندر را با شعلههای آتش، گرم میکردند و پس از ذوب شدن مواد، با فشار فلکه بالای پیستون مواد داخل سیلندر به داخل قالب، تزریق میشد و پس از سرد شدن مواد داخل قالب، گیرهها را باز و تکههای قالب را از هم جدا و محصول تولید شده را از آن خارج میکردند و تمام این مراحل با دست انجام میشد، تا زمانی که ماشینهای تزریق پلاستیک مدرن امروزی تولید شدند.
اولین دستگاه های تزریق پلاستیک که به صورت ابتدایی کار میکرد در آمریکا و در سال 1872 ساخته شد و اولین ماشین های تزریق پلاستیک پیشرفته و دارای پیچ نیز در سال 1946 در آمریکا توسط جیمز واتسون (James Watson) به ثبت رسید. وظیفه اصلی دستگاه های تزریق پلاستیک تبدیل مواد پلاستیک جامد (دانههای ریز یا گرانولهای پلیمر) به پلاستیک سیال و روان و انتقال آن به قالب میباشد به نحوی که همیشه مواد سیال آماده تزریق داخل قالب باشند.
ظرفیت ماشین های تزریق پلاستیک:
ظرفیت ماشین تزریق پلاستیک یک پرس به ماکزیمم جرمی که از پلی استیرن که در یک سیکل کاری میتوان تزریق نمود اطلاق میگردد.
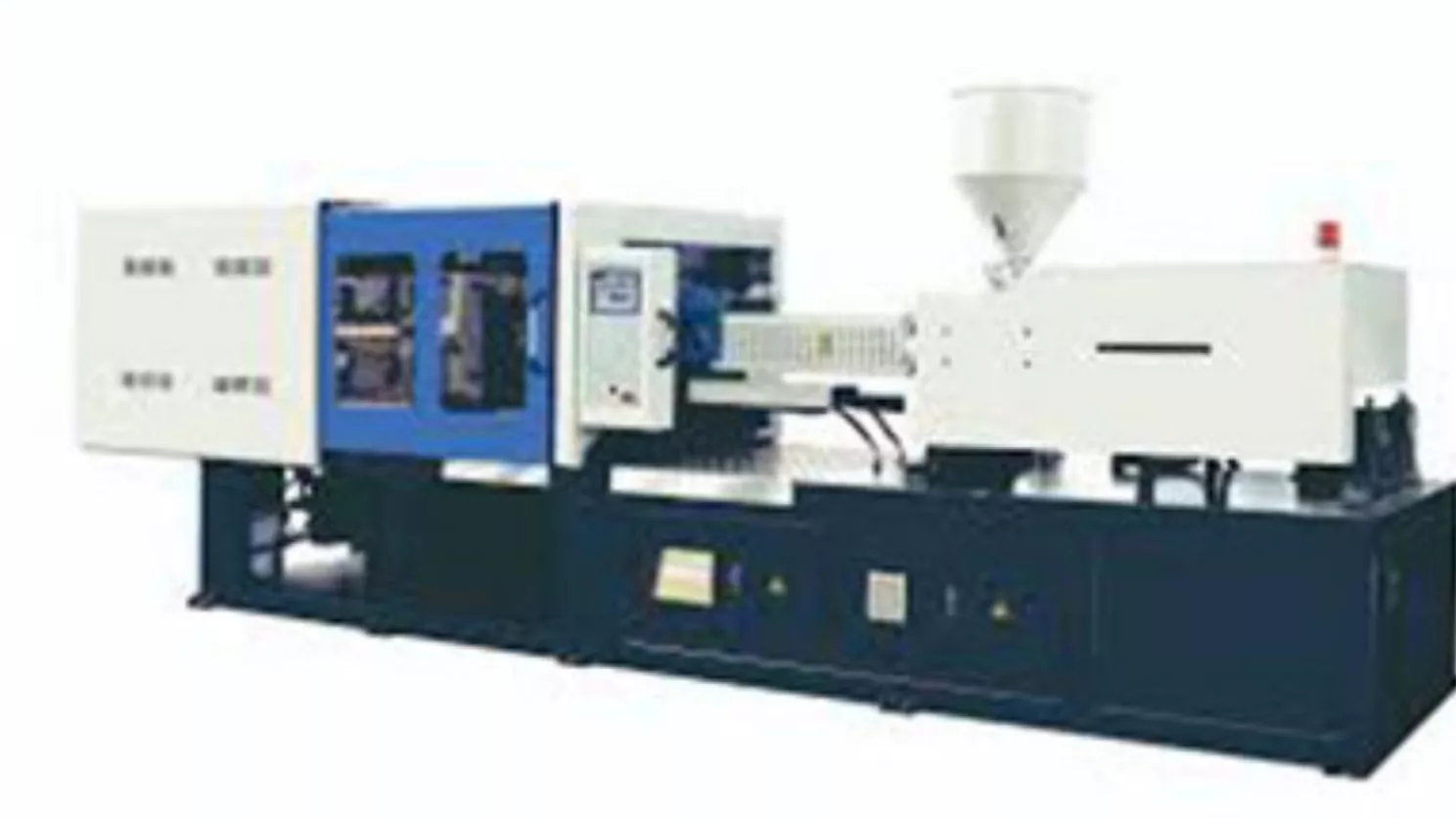
نیروی گیره کردن:
نیرویی که دو کفه قالب را به هم میچسباند نیروی گیره کردن نام دارد. قالب ماشین تزریق پلاستیک بایستی کاملاً بسته شده و سطوح سنگ زده دو کفه باید کاملاً به هم بچسبند.
انواع فشار در ماشینهای تزریق پلاستیک
فشاری که برای پر کردن قالب ماشین تزریق نیاز است را فشار تزریق میگویند.
اندازه قطعه و فرم مقطع آن، سطح راه گاهها و طول آنها، حرارت قالب، حرارت سیلندر تزریق و اندازه مدخل ورودی مواد به محفظه، تماماً در فشار تزریق اثر دارند.
وظایف ماشین های تزریق:
آماده سازی مواد قابل استفاده و فشارهای مورد نیاز مرحله تزریق.
پر كردن محفظه قالب ماشین تزریق با مواد و هدایت حركات باز كردن قالب، بیرون انداختن قطعه ریختگی و همچنین بستن و نگهداشتن قالب.
در مورد اول به عهده واحد تزریق بوده، در صورتی كه مورد سوم به وسیله واحد بستن انجام می شود.
واحد تزریق:
واحد تزریق وظیفه دارد، مواد قالب را كه بیشتر به صورت گرانول است به جلو رانده، ذوب، هموژنیزه و همچنین خمیری كرده و بالاخره به درون قالب فشار دهد.
به این منظور در یك اسكترودر حلزونی پیستونی، یك حلزون سه ناحیه ای در داخل یك سیلندر می چرخد. مواد گرانول ناحیه مكش، تراكم و رانش را طی كرده تا در محفظه جلویی حلزون به عنوان یك مذاب قابل انجام كار آماده شود.
پس از مرحله خمیری شدن، حلزونی متوقف می شود، تا اینكه به وسیله یك سیلندر هیدرولیكی با یك حركت محوری سریع تا ناحیه ۱۰۰۰mm/s، مذاب به محفظه قالب فشرده شود.
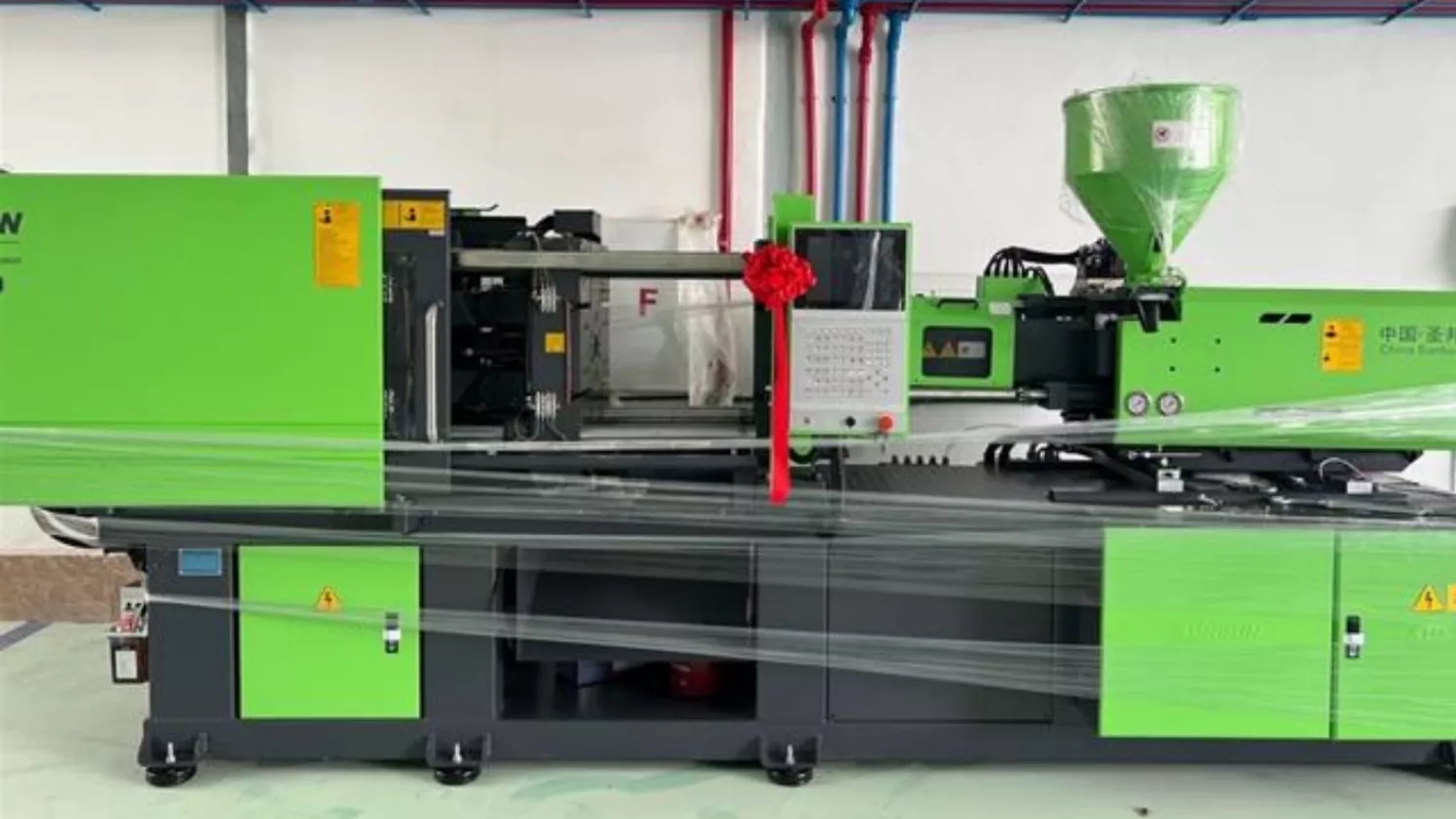
نیروی بستن- نیروی نگهداری
نیروی بستن عبارت است از نیرویی كه میلهای راهنما پس از مرحله بستن تحت تنش قرار می گیرند، میل راهنما به همان اندازه كه قالب فشرده می شود دچار افزایش طول می شود. موقع تزریق مواد یك نیروی باز كننده (FA = pw:A) FA به واسطه وجود فشار داخلی میل های راهنما را سبب می شود. مجموع نیروهایی كه موقع عمل تزریق به میل های راهنما وارد می شوند، تحت نام نیروی نگهداری عنوان می شوند. این نیور همیشه از نیروی بستن بیشتر است.
اگر نیروی باز كندنه از نیروی نگهدرای بیشتر باشد تجهیزات بین دو نیمه قالب بلند شده و مذاب از درز قالب ها بیرون زده كه منجر به ایجاد پلیسه یا تشكیل پوسته های شناور می شود. این پدیده را اضافه تزریق یا اضافه برریزی می نامند.
با وجود این باید برای جلوگیری از یك شكم دادگی صفحات حامل نیمه های قالب، مقدار نیروی نگهداری حتی الامكان در حد كم تنظیم شود. این شكم دادگی به این ترتیب ایجاد می شود كه فشار داخلی قالب را موقع تزریق سعی بر این دارد كه نیمه های قالب را در محدوده محفظه از یكدیگر جدا كند. در صورتی كه نیروهای نگهداری فقط در محدوده انتقال مستقیم نیرو موثر است. مقدار این شكم دادگی به ویژه در صفحات با صلبیت پایین و در محدوده مقابل دهانه مركزی قالب مربوطه به بخش نازل و قبل از همه در نقطه مقابل سیستم پران، زیاد است. پدیده شكم دادگی باعث تشكیل پلیسه و نیز سبب می شود كه فشار تزریق در حد بیشترین مقدار خود نتواند انتخاب شود.
یكی از روش های رفع عیب این است كه غلتک های تكیه گاهی با اضافه اندازه ۰,۰۳ mm تا ۰٫۰۵ mm در مقابل تكیه گاه های خارجی طراحی شود.
همچنین برای تخلیه هوای محفظه قالب موقع تزریق از طریق سطوح تماش نیمه های قالب، نیروی بستن باید حتی الامكان كم باشد.
اصول طراحی قطعات تزریقی
ضخامت دیوارها باید به اندازه كافی زیاد باشد تا قبل از اینكه مواد شدیداً خنك یا پخته شوند، بتوانند محفظه قالب را با اطمینان پر كنند. بنابراین باید ضخامت حداقل دیواره متناسب با طول مسیر جریان در قالب و قابلیت جریان مواد تزریق انتخاب شود.
ضخامت دیواره قطعات تزریقی باید همه جا یكسان باشد. مقدار این ضخامت در حالت معمولی ۱mm –۳mm و در قطعات بزرگ ۳mm-4mm است. ضخامت های زیر ۰,۴mm و بالای mm 8 فقط در شرایط كاری ویژه ای قابل تولید هستند.
باید از هرگونه تجمع موضعی مواد و تغییر مقطع ناگهانی پرهیز شود. زیرا این پدیده می تواند روی سطوح قطعه كار منجر به نقاط تو رفته و در داخل قطعه كار منجر به تشكیل مك شود. علاوه بر این در ضخامت های نامساوی دیواره ها درنتیجه خنك شدن غیر یكنواخت، تنش های داخلی در آن ایجاد شده كه می تواند در گوشه های تند و لبه ها به تشكیل ترك هایی منجر شود. اگر یك قطعه تزریقی باید پایداری بالاتری داشته باشد، می توان به وسیله پره های تقویت آن را عملی كرد.
برای اینكه بتوان قطعه تزریقی را به سادگی و سریع از قالب خارج كرد، تمام سطوح قطعه كار كه در جهت باز شدن قالب قرار دارند، باید شیب جزئی داشته باشند. علاوه بر این بایستی اطمینان حاصل شود كه قطعه تزریقی موقع باز شدن قالب روی نیمه مربوط به واحد بستن نشسته و به وسیله تجهیزات پران خارج شود.
مقادیر شیب در جدول ۱ فقط به عنوان مقادیر تقریبی هستند، زیرا این مقادیر نه فقط به ارتفاع قطعه تزریقی، بلكه به شكل و قطر آن، مقدار انقباض و مرحله خروج قطعه كار از قالب نیز بستگی دارد.
نازل ها
وظیفه ارتباط سیلندر تزریق و قالب به عهده نازل ها است. نازل ها طوری محكم به بوش راهگاه فشار داده می شوند كه بتوانند افزون بر این نقش در یك ماده آب بندی هم داشته باشند. علاوه بر این نازل ها باید مذاب آماده را حتی الامكان بدون اتلاف فشار و دما به محفظه قالب هدایت كنند.
در اثر تماس نازل با قالب خنك، مقدار زیادی گرما از بدنه نازل و در نتیجه از مذاب گرفته شود. استفاده از نازل حرارتی و همچنین بلند كردن نازل و قالب پس از اتمام زمان اعمال فشار نهایی اقدام موثری در این رابطه است.
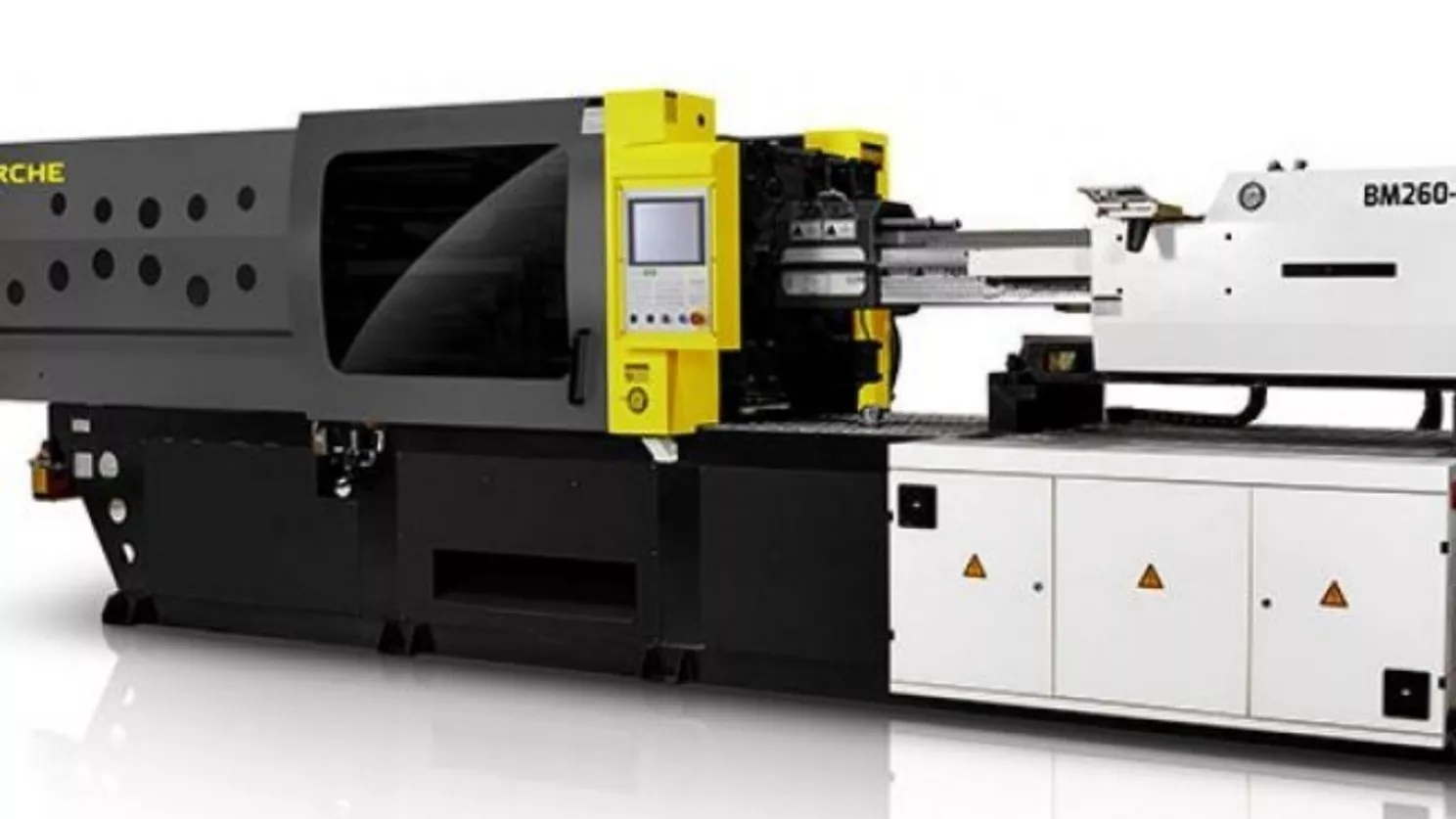
راهگاه
راهگاه یك سیستم متشكل از مسیرهای جریان است كه در آن ها مواد قابل جریان از نازل به محفظه قالب راه می یابد.
این سیستم از مخروط راهگاه، كانالهای توزیع و گلویی تزریق تشكیل می شود. در حالات ساده تر، این مسیر های جریان می تواند مثلاً یك سوراخ مخروطی كه مستقیماً به محفظه قالب منتهی می شود خلاصه گردد. نقطه اتصال راهگاه به محفظه قالب را گلویی تزریق می نامند.
شكل راهگاه باید طوری باشد كه توده مذاب از كوتاهترین مسیر ممكن و یا حداقل اتلاف گرما و فشار به محفظه قالب راه یابد. سطح مقطع مسیرهای جریان باید طوری اندازه گیری شده بانشد كه پر شدن راهگاه و همچنین محفظه قالب یكنواخت انجام شود.
شكل راهگاه ها
شكل راهگاه ها باید طوری انتخاب شود كه برای حالت ویژه، خواسته مطرح شده برآورد شود. همچنین باید به دیگر عوامل موثر نظیر اجزای قالب، مواد قالب و نوع قالب تزریق نیز توجه شود.
راهگاه ستونی یا مخروطی
راه گاه های ستونی یا مخروطی بیشتر برای قطعات ریختگی دورانی متقارن و سنگین استفاده می شوند. این راهگاه به جهت اینكه بعداً بریده می شوند، نباید روی سطوح ظاهری ایجاد شوند.
قطر D باید طوری انتخاب شود كه راهگاه همیشه از قطعه تزریقی آهسته تر خنك شود. بدین ترتیب می توان به این نكته دست یافت كه هنوز مقدار مذاب كافی دیگر می تواند با اعمال فشار نهایی یك نافی كوچك روی قطعه تزریقی باقی می ماند. به این صورت نیاز به ماشینكاری بعدی نبوده و سطحی كاری به ظاهر نامناسبی نظیر راهگاه ستونی به وجود نخواهد آمد. علاوه بر این باید راهگاه مواد را از پیش محفظه نیز نباید خارج كند.
راهگاه نقطه ای به ویژه برای قطعات كوچك و سری كاری در قالب های یك پارچه و چند پارچه و همچنین برای راهگاه های چند تایی در یك قطعه تزریقی بزرگتر در نظر گرفته می شود.
هر قدر سوراخ راهگاه نقطه ای كوچكتر باشد، به همان نسبت هم قطع شدن آن ساده تر است. در اینجا باید علاوه بر ضخامت دیواره به چقرمگی (ویسكوزیته) مذاب و همچنین دما دقت شود.
اگر محفظه قالب از طریق راهگاه نقطه ای كوچك، نتواند دیگر با سرعت كافی پر شود، مذاب در پیش محفظه زودتر خنك شده، طوری كه تحت شرایطی باید با دست خارج شود.
به این ترتیب پیش محفظه كمی بزرگتر می شود، طوری كه مواد خنك شده چسبیده به جدار داخلی به عنوان یك لایه عایق عمل می كند. هسته مذاب (به اصطلاح بستر خمیری) در محدوده راهگاه به صورت مایع باقی می ماند. اما تاخری زمانی مذاب در پیش محفظه نباید طولانی باشد. حداقل چهار تا پنج تزریق در دقیقه برای عملگرد این سیستم لازم است.
در جایی كه این توالی تزریق امكان پذیر نیست، یك كلگی مسی سوراخ شده در پیش محفظه گذاشته می شود. فضای بنی كلگی مسی و جداره داخلی پیش محفظه با مواد خنك شده پر و به عنوان عایق پیش محفظه با مواد خنك شده پر و به عنوان عایق عمل می كند. كلگی مسی از طریق نازل، گرمای كافی دریافت كرده تا مواد میانی را به صورت مذاب نگه دارد.