رایجترین کورههای ذوب آهن و فولاد که در اکثر کارخانهها مورداستفاده قرار میگیرند شامل کوره بوتهای، کوره کوپلا، کوره القایی و کوره الکتریکی میشوند. هرکدام از این کورهها، تکنولوژی منحصربهفرد خود را دارند که آنها را برای شرایط و ظرفیتهای تولیدی متفاوت مناسب میکند.
علاوه بر کورههای یادشده که برای ذوب فلزات بهمنظور ساخت قطعات استفاده میشوند، کورههای دیگری نیز وجود دارند که برای استخراج فلزات از سنگ معدن آنها به کار برده میشوند. این کورهها شامل کوره رو باز، کوره بسمر، کوره اکسیژن قلیایی و کوره بلند میشوند که اغلب برای آهنسازی و تولید فولاد مورداستفاده قرار میگیرند. در مقاله تولید فولاد، با این کورهها و روشهای فولادسازی بیشتر آشنا شوید.
کوره بوته ای
کورههای بوتهای اغلب برای ذوب آلیاژهای غیرآهنی که نقطه ذوب پایینی دارند به کار برده میشوند. مکانیزم این کورهها نیز شامل استفاده از یک پاتیل سرامیکی نسوز است تا در هنگام مواجهه با دمای بالا، بتوانند مقاومت کنند. این پاتیل سرامیکی که بوته نام دارد، در بالای منبع حرارت قرار میگیرد تا فلز و مواد افزودنی موجود در آن ذوب شود. اندازه این بوتهها متفاوت است.
این نوع کوره ذوب دارای ساختار محصور شده است تا حرارت در درون آن نگه داشته شود. سوختهای مصرفی رایج برای کوره بوتهای نیز شامل زغالسنگ یا گاز طبیعی میشوند. در طراحی و سیستم گرمایش کورهها نیز تفاوتهایی وجود دارد. بهغیراز کورههای بوتهای متحرک و ثابت، کورههای بوتهای کج و ثابت نیز وجود دارند. همچنین باید بین کورههای مقاوم در برابر گرمایش و گرمایش با سوخت تفاوت قائل شد.
انواع کوره بوته ای رایج در صنایع ریختهگری عبارتاند از:
1. کوره بوتهای ثابت: پاتیل درون این نوع کوره ثابت است و فلز مذاب با استفاده از یک شیر در کف کوره از آن خارج میشود.
2. کوره بوتهای متحرک بالابر: زمانی که فلز داخل بوته کاملاً ذوب شد، پاتیل را با کمک جرثقیلهای داخل محل تولید بالا میبرند تا فلز مذاب به قالبها برسد.
3. کوره بوتهای کج: پاتیل درون کوره ثابت است و کل سیستم کوره کج میشود تا فلز مذاب از آن خارج شود.
کوره کوپلا
کوره کوپلا از مدتهای بسیار طولانی در صنایع ریختهگری مختلف استفاده میشده است. مشخصه بارز این نوع کوره، ارتفاع بلند و دودکشهای استوانهای شکل است. درون آن از لایههایی از رس و آجر بهمنظور محافظت از بخشهای داخلی در برابر حرارت شدید، سایش و اکسایش تشکیل شده است. این کوره برای تولید تناژ بالا از مذاب بسیار مناسب است و اغلب برای ذوب چدن استفاده میشود.
برای فرآیند ذوب نیز، چندین لایه فرو آلیاژها، کک و سنگآهک قبل از اینکه فلز اصلی اضافه شود، به درون کوره شارژ میشوند. درنتیجه، این مواد در اثر حرارت واکنش داده و بهصورت ناخالصی بر روی سطح مذاب معلق میشوند. وظیفه و کارایی این مواد افزودنی عبارتاند از:
1. کک: بهعنوان سوخت برای ذوب مواد درون کوره استفاده میشود.
2. قراضه و عناصر آلیاژی: مواد شارژی اصلی که مذاب فلزی را تشکیل میدهند.
3. سنگآهک: افزودن این ماده که فلاکس نیز نامیده میشود، منجر به واکنش خاکستر و ناخالصیهای دیگر با آن شده که سرباره را تشکیل میدهند. نقش این سرباره مذاب که بر روی فلز مذاب قرار میگیرد، جلوگیری از اکسایش سطحی فلز مذاب است.
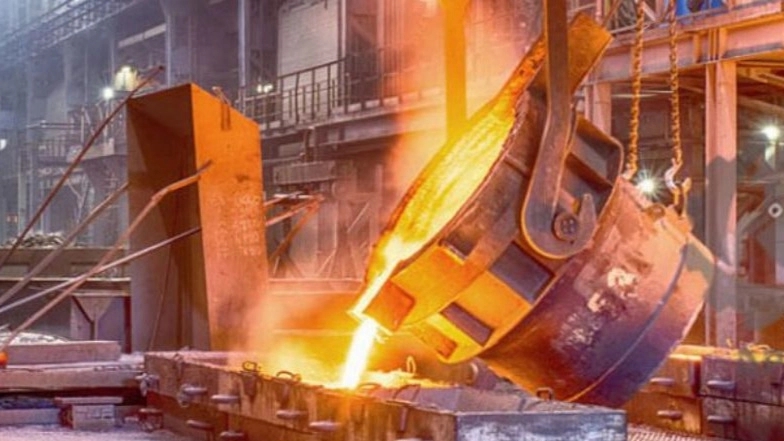
کوره القایی
کورههای القایی از طریق تکنولوژی القای جریان الکترومغناطیسی متناوب، حرارت و دمای لازم برای ذوب فلزات و آلیاژها را تأمین میکنند. این میدان الکترومغناطیسی، سبب ایجاد جنبش در اتمهای فلزات شده که درنهایت منجر به تولید حرارت میشود. منبع جریانهای الکترومغناطیسی، کویل یا سیمپیچهای مسی هستند که در اطراف قطعه قرار میگیرند اما با آن تماس فیزیکی ندارند. این نوع کورهها به دلیل تولید مذاب با کیفیت بالا، نگهداری آسان و بازده انرژی بسیارخوب، یک گزینه ایدئال برای صنایع ذوب و ریختهگری هستند.
کوره الکتریکی
کورههای قوس الکتریکی یکی از بزرگترین کورههای ذوب و ریختهگری هستند که میتوانند فلز مذاب را تا ۲۵ الی ۴۵ تن در ساعت تولید کنند. به همین دلیل از آنها برای تولید تناژ بالا در ریختهگری استفاده میشود. اصل کار کورههای قوس الکتریکی بسیار آسان است. یک قوس الکتریکی که از الکترودهای کربنی ناشی میشود، با ایجاد جریان الکتریکی، گرما تولید میکند. در عمل، کورههای قوس الکتریکی عمدتاً برای ذوب ضایعات فولادی بهمنظور تولید محصولات جدید، استفاده میشوند.